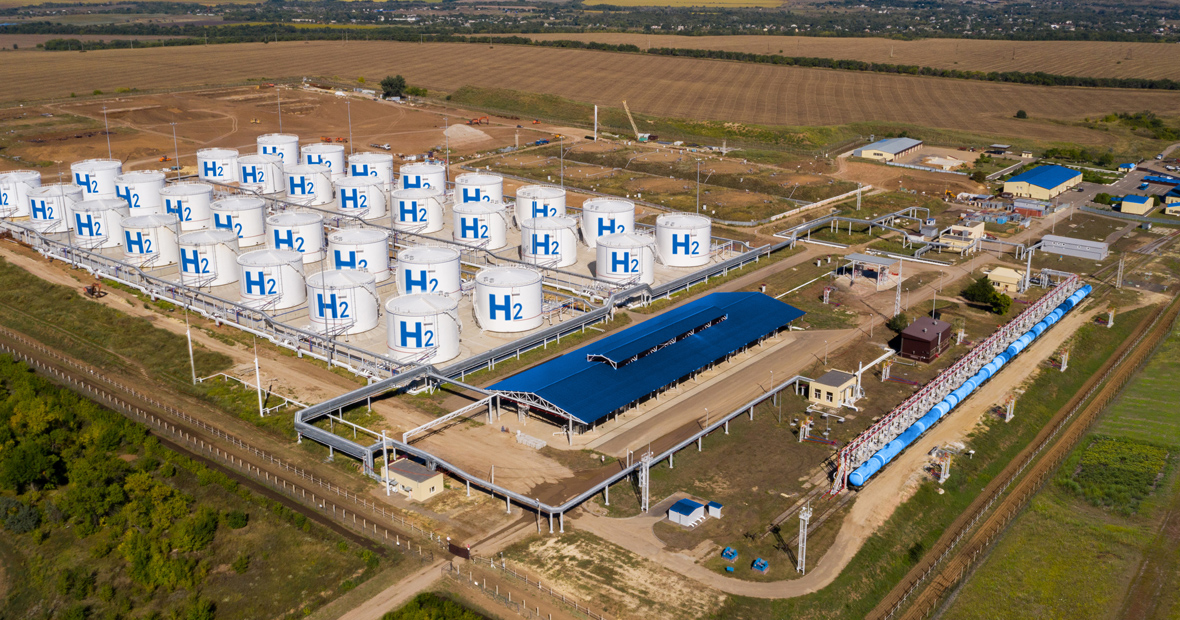
Hydrogen generators are at the forefront of clean energy technology, offering innovative solutions for producing this versatile fuel. As the world shifts towards sustainable energy sources, understanding the various types of hydrogen generators becomes increasingly important. These devices play a crucial role in sectors ranging from industrial processes to renewable energy storage, each with unique advantages and applications.
Electrolysis-based hydrogen generators: principles and technologies
Electrolysis stands as a cornerstone in hydrogen production, utilizing electricity to split water molecules into hydrogen and oxygen. This process forms the basis for several types of hydrogen generators, each with its own unique characteristics and efficiencies. The principle of electrolysis is straightforward, but its implementation varies significantly across different technologies. You may find here more information.Proton exchange membrane (PEM) electrolysis systems
PEM electrolysis represents a cutting-edge approach to hydrogen generation. These systems use a solid polymer electrolyte membrane to facilitate the separation of hydrogen and oxygen. The key advantage of PEM technology lies in its ability to produce high-purity hydrogen at high pressures, making it ideal for applications requiring clean, compressed hydrogen. PEM electrolyzers operate efficiently at lower temperatures compared to other electrolysis methods. This characteristic allows for rapid start-up and shutdown, making PEM systems particularly suitable for integration with renewable energy sources like wind and solar power. The flexibility of PEM electrolyzers in handling variable power inputs contributes to their growing popularity in green hydrogen production.PEM electrolysis systems are revolutionizing on-site hydrogen production, offering a compact and efficient solution for diverse applications from industrial processes to fuel cell vehicle refueling stations.
Alkaline electrolysis: High-Capacity industrial production
Alkaline electrolysis is one of the most established methods for large-scale hydrogen production. This technology utilizes a liquid alkaline solution, typically potassium hydroxide, as the electrolyte. Alkaline electrolyzers are known for their robustness and ability to handle high-capacity production needs, making them a staple in industrial hydrogen generation. The primary advantages of alkaline electrolysis include lower capital costs and the ability to operate continuously for extended periods. These systems are particularly efficient when running at constant power, making them ideal for baseload hydrogen production in industrial settings. However, they generally operate at lower current densities compared to PEM systems, resulting in larger footprints for equivalent hydrogen output.Solid oxide electrolyzer cells (SOEC) for High-Temperature electrolysis
Solid Oxide Electrolyzer Cells represent an advanced form of electrolysis that operates at significantly higher temperatures than PEM or alkaline systems. Typically functioning at temperatures between 700°C and 900°C, SOECs leverage this heat to enhance the efficiency of the water-splitting process. The high-temperature operation allows for a portion of the energy input to be supplied as heat rather than electricity, potentially increasing overall system efficiency. SOECs use a solid ceramic electrolyte, which becomes conductive to oxygen ions at high temperatures. This unique characteristic allows for the production of not only hydrogen but also syngas, a mixture of hydrogen and carbon monoxide, when carbon dioxide is introduced alongside water vapor. The versatility of SOEC technology makes it particularly interesting for applications in sectors like synthetic fuel production and industrial processes requiring both hydrogen and carbon monoxide.Thermal decomposition hydrogen generators
Thermal decomposition methods offer alternative pathways for hydrogen production, utilizing heat to break down various feedstocks into hydrogen and other byproducts. These processes can leverage high temperatures from renewable sources or industrial waste heat, presenting opportunities for efficient and sustainable hydrogen generation.Solar thermochemical hydrogen production
Solar thermochemical hydrogen production harnesses the intense heat of concentrated sunlight to drive chemical reactions that yield hydrogen. This innovative approach typically involves a two-step process using metal oxides. In the first step, high temperatures reduce the metal oxide, releasing oxygen. The second step reoxidizes the reduced metal with steam, producing hydrogen. The potential of solar thermochemical processes lies in their ability to achieve high efficiencies by directly converting solar energy to chemical energy in the form of hydrogen. This method bypasses the efficiency losses associated with electricity generation, potentially offering a more direct and efficient path to solar hydrogen production.Thermocatalytic decomposition of methane
Thermocatalytic decomposition of methane, also known as methane pyrolysis, offers a unique approach to hydrogen production that doesn't generate CO2 as a byproduct. This process involves heating methane to high temperatures (typically above 700°C) in the presence of a catalyst, causing it to break down into hydrogen and solid carbon. The solid carbon byproduct, often in the form of carbon black or graphite, can be used in various industrial applications or sequestered, making this method attractive from a carbon management perspective. TheCH4 → C + 2H2
reaction presents an opportunity for hydrogen production with a significantly reduced carbon footprint compared to traditional methane reforming processes.
Biomass gasification for hydrogen generation
Biomass gasification represents a renewable approach to hydrogen production, utilizing organic materials as feedstock. The process involves heating biomass to high temperatures (typically 700-1000°C) in a low-oxygen environment, producing a synthesis gas (syngas) rich in hydrogen and carbon monoxide. This syngas can be further processed to increase hydrogen yield through water-gas shift reactions. The advantage of biomass gasification lies in its ability to utilize a wide range of organic waste materials, from agricultural residues to municipal solid waste. This flexibility makes it an attractive option for sustainable hydrogen production, especially in regions with abundant biomass resources. However, challenges remain in optimizing process efficiency and managing feedstock variability.Photobiological and photoelectrochemical hydrogen production
Nature's own processes for hydrogen production inspire innovative technologies that harness light energy directly for hydrogen generation. These methods, while still largely in the research and development phase, hold promise for sustainable, low-impact hydrogen production.Algal hydrogen production: chlamydomonas reinhardtii systems
Certain species of green algae, notably Chlamydomonas reinhardtii , possess the remarkable ability to produce hydrogen through photobiological processes. Under specific conditions, these microorganisms can redirect their photosynthetic machinery to generate hydrogen instead of fixing carbon dioxide. This process occurs when algae are deprived of sulfur, triggering a switch from oxygen to hydrogen production. The potential of algal hydrogen production lies in its direct conversion of solar energy to hydrogen, bypassing the need for electrolysis. However, current challenges include low hydrogen production rates and the need for carefully controlled conditions. Ongoing research focuses on genetic engineering and process optimization to enhance the efficiency and scalability of this biohydrogen production method.Tandem cell photoelectrochemical water splitting
Tandem cell photoelectrochemical (PEC) water splitting represents an advanced approach to solar hydrogen production. This technology utilizes specialized semiconductors to absorb light and drive the water-splitting reaction directly. Tandem cell designs incorporate multiple light-absorbing layers to capture a broader spectrum of solar energy, potentially increasing overall system efficiency. In a typical tandem PEC cell, one semiconductor drives the oxygen evolution reaction, while another facilitates hydrogen evolution. The key advantage of this approach is the potential for high solar-to-hydrogen conversion efficiencies, theoretically surpassing those of separate photovoltaic-electrolysis systems. However, challenges remain in developing stable, efficient, and cost-effective materials for large-scale implementation.Dye-sensitized photoelectrochemical cells
Dye-sensitized photoelectrochemical cells offer a unique approach to solar hydrogen production, inspired by natural photosynthesis. These systems use organic dyes to absorb light and initiate the water-splitting process on semiconductor surfaces. The dye molecules act as photosensitizers, expanding the light absorption range of the semiconductor and potentially improving overall efficiency. The appeal of dye-sensitized systems lies in their potential for low-cost manufacturing using abundant materials. Current research focuses on developing stable and efficient dye-semiconductor combinations and optimizing cell architectures for improved hydrogen production rates. While still primarily in the research phase, this technology holds promise for scalable, aesthetically pleasing solar hydrogen generation solutions.Steam methane reforming (SMR) hydrogen generators
Steam Methane Reforming (SMR) remains the most widely used method for industrial hydrogen production, accounting for a significant portion of global hydrogen supply. This process involves reacting methane (natural gas) with high-temperature steam to produce hydrogen, carbon monoxide, and a small amount of carbon dioxide.Conventional SMR process and catalysts
The conventional SMR process occurs in multiple stages. Initially, methane reacts with steam over a nickel-based catalyst at temperatures around 700-1000°C, producing a syngas mixture of hydrogen and carbon monoxide. This reaction is highly endothermic, requiring significant heat input. The resulting syngas then undergoes a water-gas shift reaction to convert carbon monoxide to additional hydrogen and carbon dioxide. Catalyst development plays a crucial role in optimizing SMR efficiency. Modern catalysts aim to improve reaction kinetics, reduce coking (carbon deposition), and enhance durability under high-temperature conditions. Research continues to focus on developing catalysts that can operate at lower temperatures or with increased resistance to sulfur poisoning, a common issue in natural gas feedstocks.Autothermal reforming (ATR) technology
Autothermal Reforming (ATR) represents an evolution of the SMR process, combining partial oxidation with steam reforming. In ATR, oxygen is introduced alongside steam and methane, allowing some of the methane to combust. This combustion provides the heat necessary for the endothermic reforming reactions, potentially reducing external heating requirements. The key advantage of ATR lies in its ability to produce a hydrogen-rich syngas with a lower H2/CO ratio compared to conventional SMR. This characteristic makes ATR particularly suitable for applications requiring syngas, such as Fischer-Tropsch synthesis or methanol production. Additionally, ATR units typically have a smaller footprint than equivalent SMR plants, offering advantages in terms of capital costs and space requirements.Carbon capture and storage in SMR processes
As the world moves towards decarbonization, integrating carbon capture and storage (CCS) technologies with SMR processes has gained significant attention. CCS in SMR aims to capture the CO2 produced during the reforming and shift reactions, preventing its release into the atmosphere. Various capture technologies are being explored, including pre-combustion capture, post-combustion capture, and oxyfuel combustion. Implementing CCS in SMR processes presents both challenges and opportunities. While it significantly reduces the carbon footprint of hydrogen production, it also increases complexity and cost. Current research focuses on developing more efficient capture technologies and exploring ways to utilize the captured CO2, such as in enhanced oil recovery or the production of synthetic fuels.The integration of CCS with SMR processes represents a crucial step towards producing "blue hydrogen," offering a transitional solution in the journey towards fully renewable hydrogen production methods.